Signs It’s Time For Your Conveyor Rollers Replacement
Conveyor systems are designed to last a long time, depending on how well you maintain them. However, it’s possible to ignore the telltales of its wear and tear as most people are guilty of overestimating the longevity of machines. You could continue wasting a lot of money on repairing components that are already past their better days. So, what signs should tell you that you need conveyor rollers replacement?
Excessive repairs and maintenance
Regular unscheduled maintenance problems gradually turn into huge and silent expenses. Once you start repairing adjacent components working within the conveyor rollers, consider replacing the entire system together with its adjacent elements.
There are better rollers in the market
Lack of current technology and advancement could be hitting you with hidden opportunity costs. The industry keeps evolving by the day, paving the way for more products that work efficiently. Better working rollers will save you money and time in the long-run. If you come across better rollers that will increase productivity in your plant, you have a valid reason to replace them.
You can’t find spare parts
There are times when your conveyor rollers will stop working due to defective parts. If your conveyor system is old or rare, you may find a hard time tracing these tiny spare parts that give the rollers their relevance. In such a case, you will have no other options but to seek an entire conveyor roller replacement as a whole, together with all its working parts.
Broken rollers
Accidents, wear, and tear can all break the conveyor rollers. Such defects warrant an immediate conveyor rollers replacement before the entire system continues to deteriorate.
Have you noticed any of these signs in your conveyor? Call us today for professional inspection and consultation on the best move forward. We are here to serve you.
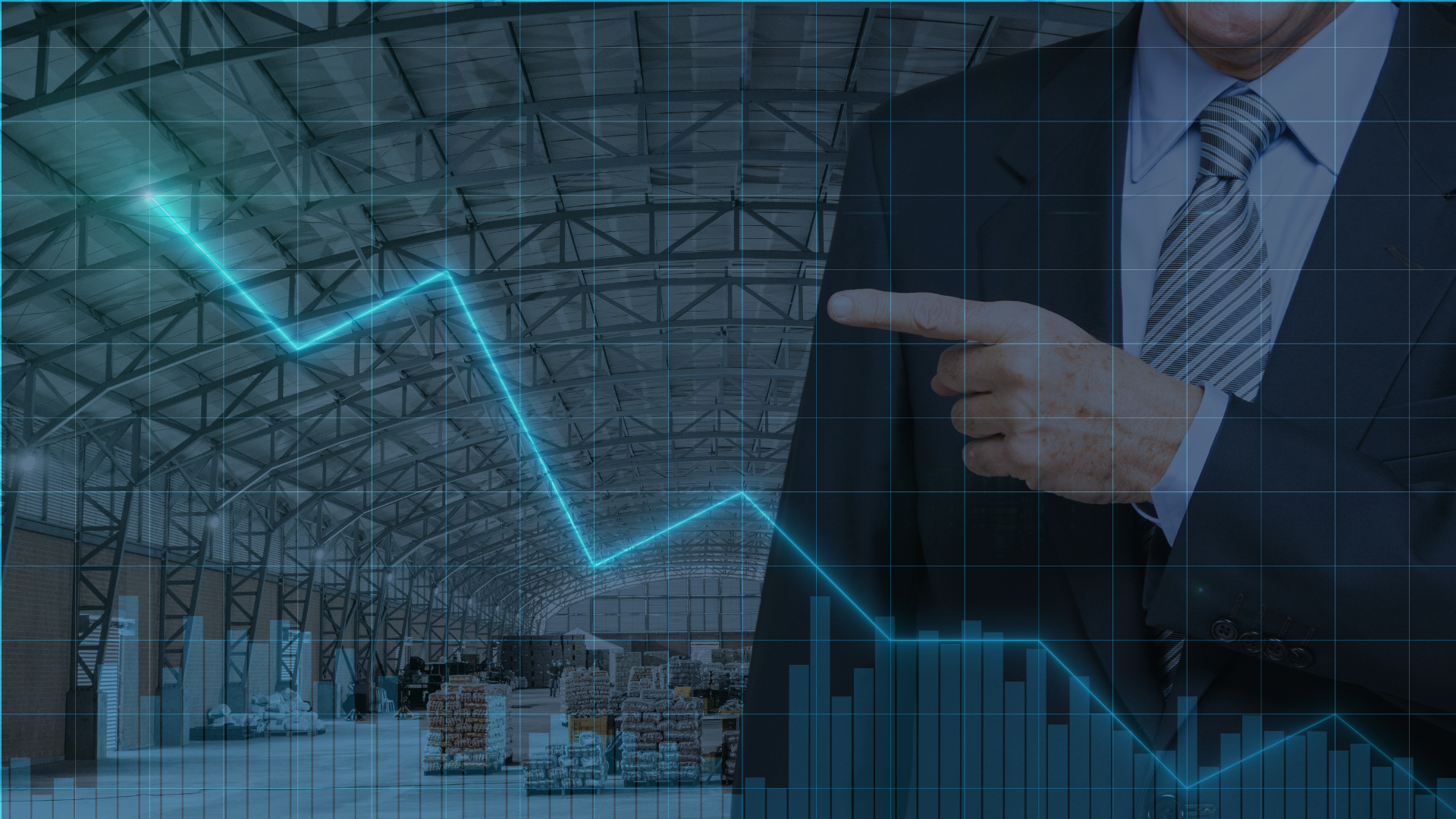
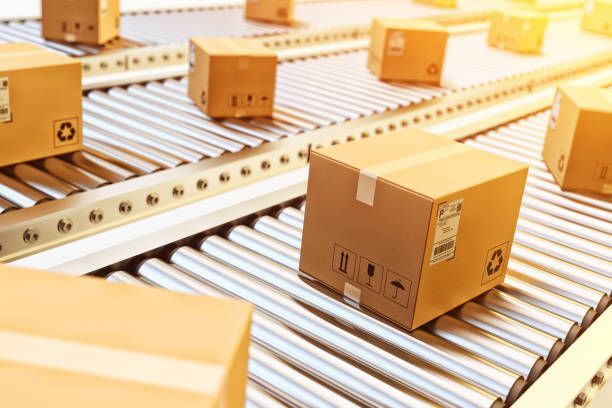
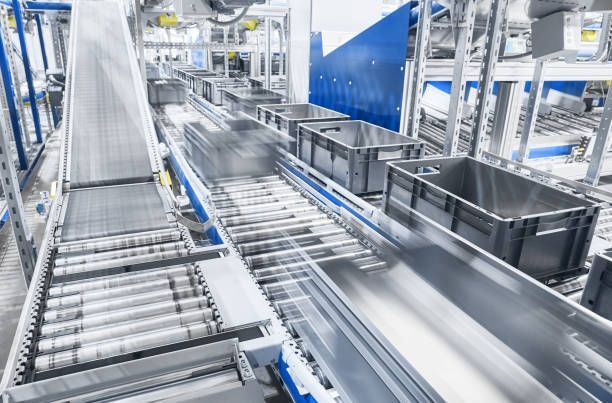
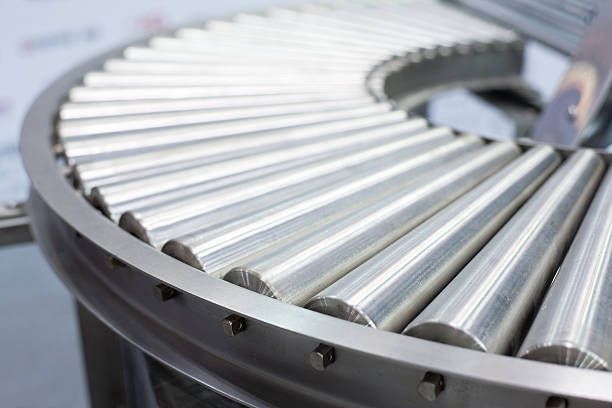