5 Ball Bearings Used In Conveyor Rollers
Mobility in engineering is a vital element, and many manufacturing businesses and industrial processes require movement of inventory, materials, finished goods, and other objects within parameters. Conveyor rollers have around for quite some time, and they provide tremendous utility to such ventures.
Furthermore, with their open-ended trays that can be joined to create any pathway along with the ability to be customized to fit any floor plan, conveyor rollers have limitless potential to be adapted to your requirements.
According to a recent study by Fortune Business Insights, the global conveyor systems market size was around $5.23 billion in 2019 and is projected to reach $7.43 billion in 2027. This brings the growth rate of 4.5% CAGR during the forecasted period.
The driving forces behind this increase are the transformations in the e-commerce industry and traditional supply chains. This is compelling for companies to change the way they move, track, and store materials using automation and other advanced technologies.
With that out of the way, let’s take a quick look at some of the best ball bearings used in conveyor rollers around the globe.
Angular Contact Ball Bearings
The angular contact ball bearings are designed and developed to have an inner and outer ring raceway that is positioned relative to each other in the direction of the bearing axis. This allows them to accommodate combined loads while simultaneously acting axial and radial loads.
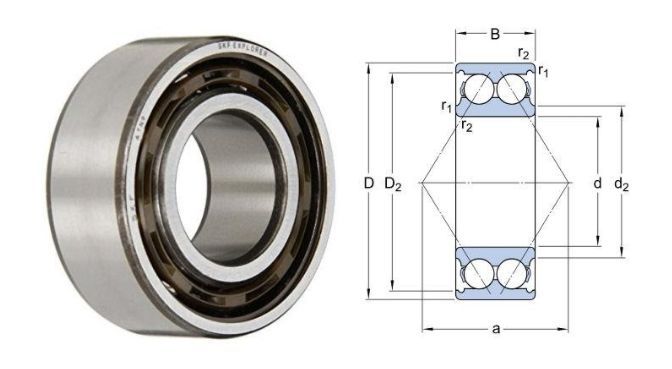
The angular contact ball bearings are used to support conveyor belt rolling shafts. These are long cylindrical structures that form the main section of the conveyor belt and have the ability to roll and manage weight of the workload.
As the contact angel increase the axial load capacity of angular contact ball bearings also increases. There are several variations available including single row angular contact ball bearings, double row angular contact ball bearings, and four-point contact ball bearings, with each of them offering their own benefits.
Deep Groove Ball Bearing
Widely considered as one of the most commonly used and conventional types of ball bearings , deep groove ball bearings are used for a variety of applications. One popular variation is the single-row deep groove ball bearings that have steel shields and rubber seals installed on one or both sides while requiring prepublication with grease.
These bearings can be used in multiple quantities to create conveyor belt systems as shown in the picture.
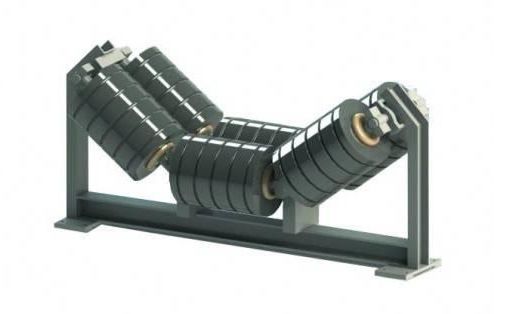
Snap rings are sometimes used on the periphery whereas for big deep groove ball bearings. Machined brass cages are used since machined cages are adequate for high-speed applications.
These types of bearings are also quite versatile due to their low friction and are optimized low noise and low vibration as well as requiring less maintenance than other bearing types.
Pillow Block Bearing
Also known as plummer block , pillow block bearing is a pedestal that can be used to provide support for a rotating shaft with the help of various accessories and compatible bearings.
The assembly consists of a mounting block which houses a bearing. The insert bearing mounted in the housing can be bolted to a support surface.
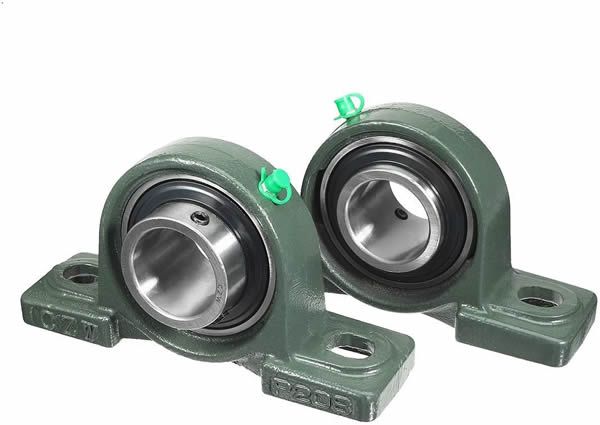
Pillow block bearings are housing bearings that act like a pedestal which is used to support the rotating shaft of conveyor belts with other compatible bearings.
These bearing types are commonly used in the most demanding food and beverage related environments. The inside of the bearing is typically 0.025 mm larger than the shaft to ensure a tight fit. Housing material for pillow block bearings is mostly made from cast iron or cast steel.
Self-Aligning Ball Bearings
Self-aligning ball bearings are made available either open or sealed. They have two rows of balls along with a common sphered raceway in the outer right and two deep uninterrupted raceway grooves in the inner ring.
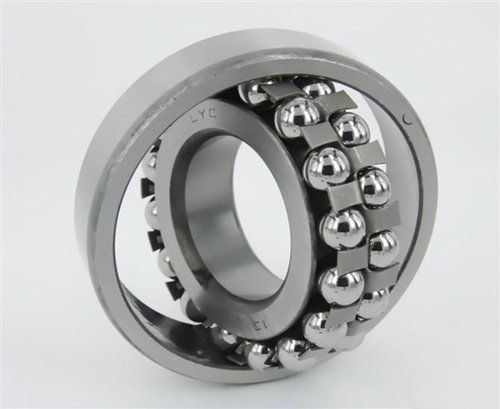
This allows the axis of the inner ring, balls and cage to deflect around the bearing center to automatically correct misalignment caused by housing and shaft machining or installation error.
Hence this makes these types of bearings to be insensitive to angular misalignment of the shaft relative to the housing, which can be caused by shaft deflection.
These bearings are used in similar fashion as the angular contact bearings. However the only difference is that they can only be used in light axial load applications due to the small axial capacity.
Tapered Roller Bearing
They are commonly used for heavy-duty applications with moderate speed and where durability is required. They are rolling element bearings that can support axial forces as well as radial forces making them good thrust bearings.
The inner and outer ring raceways are segments f cones, and the rollers are tapered so that the conical surfaces of the raceways and roller axes would meet at a common point on the main axis of the bearing.
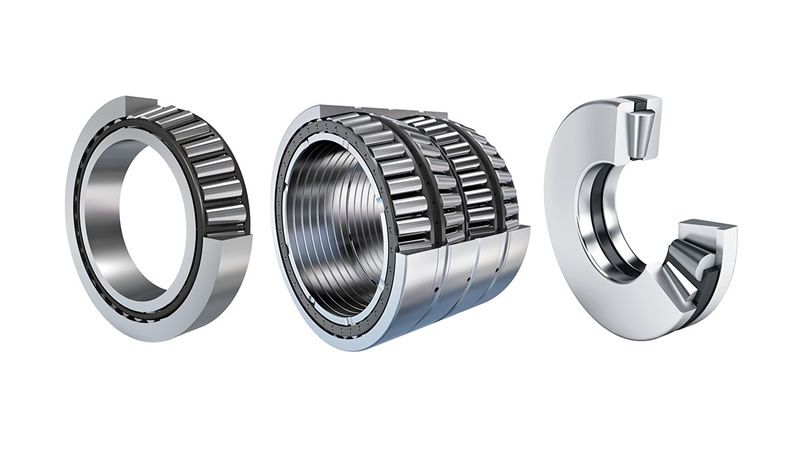
Due to the overall geometry, the motions of the cones remain coaxial with no sliding motion between raceways and the OD of the rollers. Engineering students often request for a personal statement help when dealing with topic involving tapered roller bearings and other types of bearings.
Tapered roller bearings can substitute for other types of bearings mentioned in this list apart from Pillow Block Bearings. They are usually implemented to support for moderate speed but heavy duty applications where durability is priority.
Conclusion
Conveyor systems are one of the best when it comes to handling equipment that transports materials from one pace to another. Their usefulness comes with the ability to move and feed the system making the process convenient, easier, and faster with the ability to withstand large workloads and even extreme weather conditions.
Powering these systems are the ball bearings which offer relatively easy replacement with increase motor performance through less motor friction and the ability to withstand a wide range of temperatures from -40 to 180 degrees.
However, bearing selection is often done, keeping in mind the load and the working environment.
Author Bio
Claudia Jeffrey currently works as a Content Strategist at Dissertation Assistance. This is where higher education students can acquire dissertation proposal service from experts specializing in their field of study. During her leisure time, she likes to travel with her family and friends to discover exotic new locations.
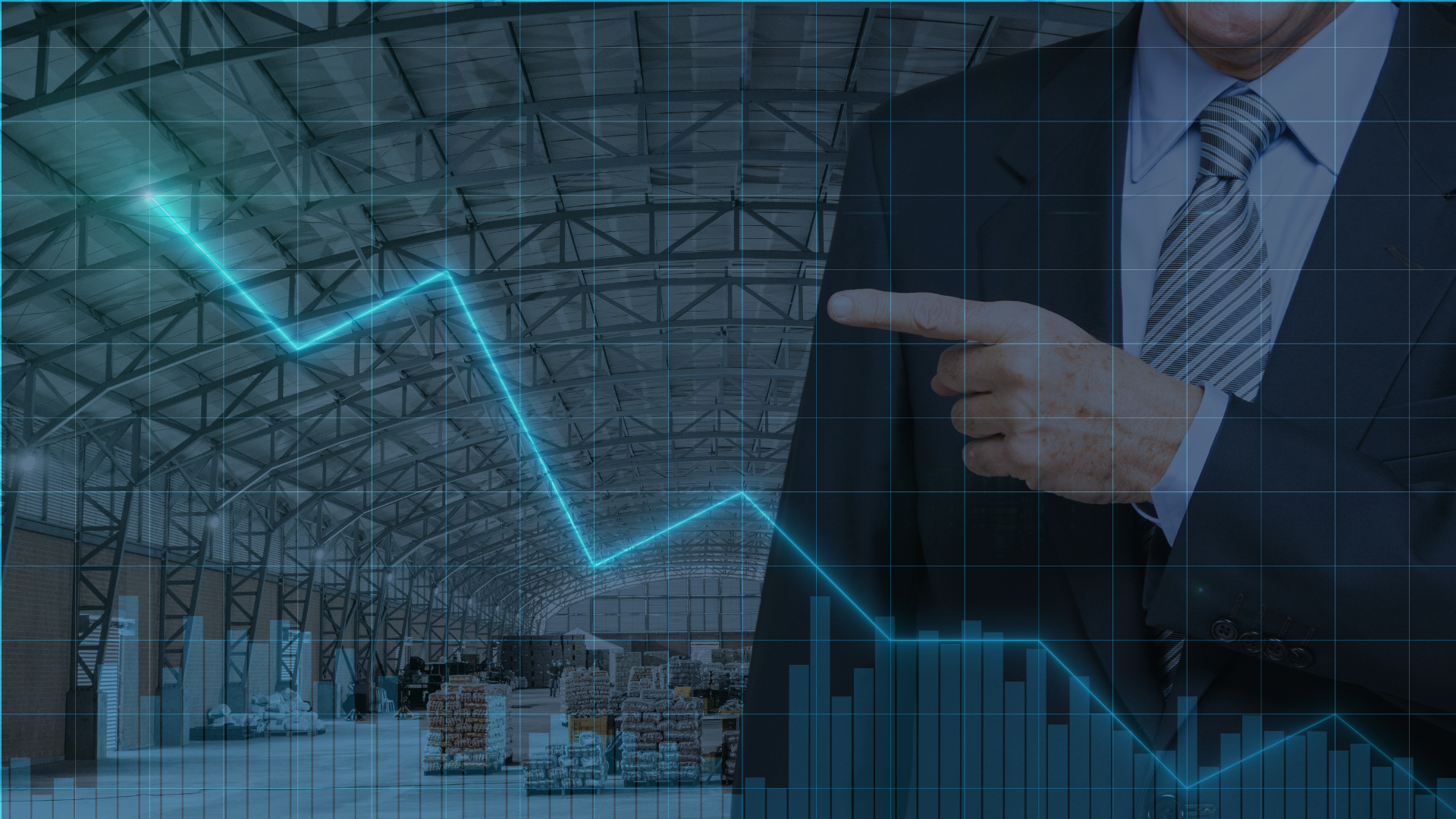
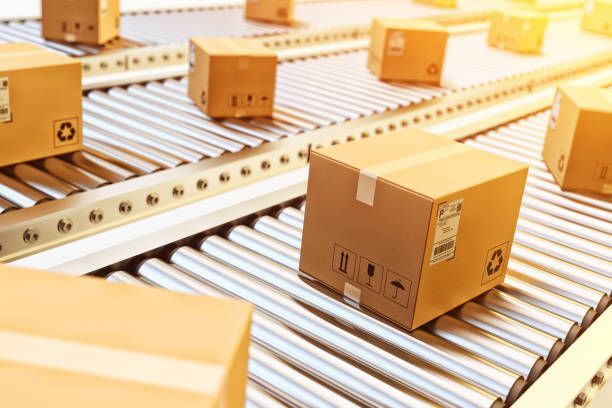
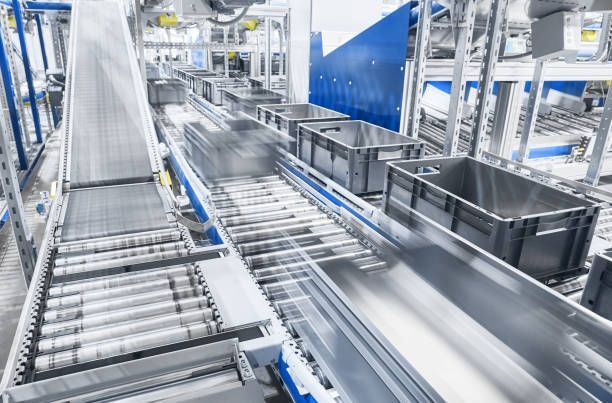
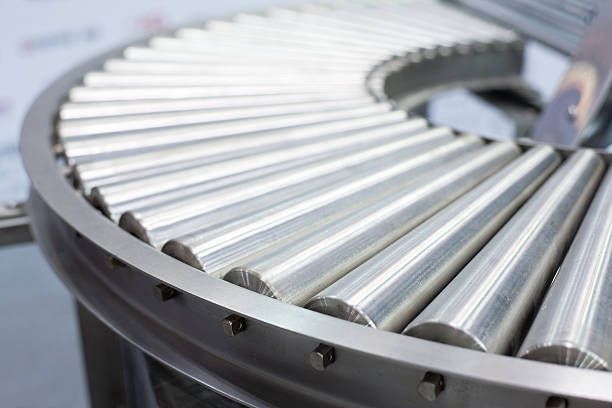